Disclaimer: This study is a work for creating awareness amongst general public and other stakeholders on safety and hazards in a Microcrystalline Cellulose manufacturing and storage plant.
The study deals with the hazardous substances used, process involved and hazards involved in various process segments of the plant. The present study is based on data available in the Annual Report, Marketing, Advertising reports of Sigachi industries, literature survey and equipment vendor literature.
A. Accident Brief:
In the morning of 30th June 2025 @ 9.00 am a Fire and Explosion occurred in the Micro Crystalline Cellulose Production Plant of Sigachi Industries ,Pashamylaran, Telengana state of India. 40 workers have died and 33 workers injured in the above Fire and Explosion. Causes of the accident are being investigated by the competent authorities. The present analysis aims to create an awareness about such incidents and does not proclaim as an authentic report or to divert / influence issues of the accident.
B. Brief Process Description:
Stepwise processing steps are given as under:
1. Sheets of wood pulp are added to glass lined reactors, for hydrolysis of the wood pulp which is carried out at the required temperature and pressure.
2. The slurry is then sent for filtration. At filter press, the slurry is passed through in to separate ‘mother liquor’ from the slurry and the ‘filtrate’ is sent to the effluent treatment plant. The residual cake is washed during the process to make it neutral as well as salt free. Air is passed through the cake to reduce the moisture content.
3. As per author’s understanding Spray Drying is used to dry the cake into Micro Crystalline Cellulose. In Spray Drying step the cake is sprayed at high pressure around 70 Bar to ensure atomisation through nozzles to feed in the spray dryer where drying takes place using hot air at a pressure of 4-7 Bar.The product obtained from spray drying process is sieved and directly sent for packaging.
4. The final product is packed in as specified by the customers. Once the packaging is done, the final products are then transferred to quarantine room for testing, then transferred to finished goods storage area.
As data for the plant are not available, based on process engineering experience, the author has developed following Process Flow Diagram.
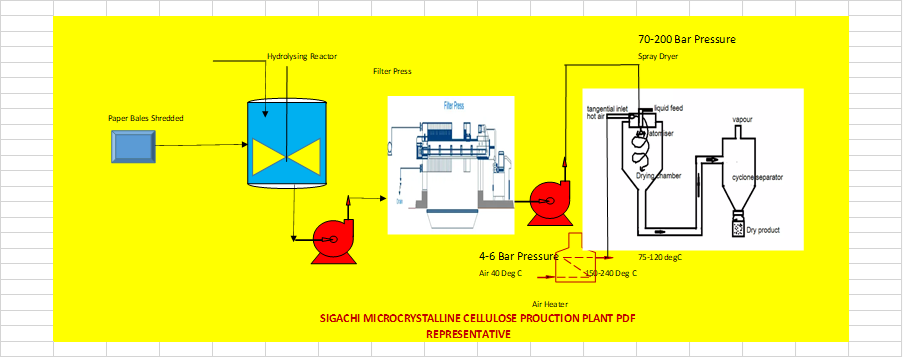
C. Potential Hazards of the Plant:
Hazardous Substances:
c.1 Micro Crystalline Cellulose(MCC)
c.2 Hydrocarbons used in the furnace to heat Air
c.3 High pressure Cellulose cake
Process Hazards:
c.4 Process Conditions in the furnace
c.5 Process Conditions in Spray Dryer
c.6 Process Conditions in Cyclone Separator /quarantine storage
Hazardous Substances:
C. 1 Microcrystalline Cellulose (MCC)
- Microcrystalline Cellulose is refined wood pulp and it is a chemically inert substance.
- Molecular Formula C6H10O5N
- Particle size distribution D10<45 Microns, D50 70-100 micron, D90>140 Microns.
- MCC size 15 to 250 microns. Excess dust generation can create explosion hazard.
- Explosive powder concern range 100 g/m3 to few kg/m3 @<=420 microns
- Auto ignition Temperature 3990C
- Damp Cellulose can be significant fire hazard as it can go for spontaneous combustion.
- Minimum Energy for Ignition is 35 m J.
- Bulk Density: 200-600 kg/m3.
- Conductivity max 75 Micro Siemen
- Explosion Severity Indexes
Explosion Hazard Class | Combustion Explosion Severity Index .KST, Bar-m/s | Explosion Power | Substance |
St1 | 200-300 | Strong | Cellulose |
This hazard will be further analysed in various nodes of the process.
C.2 Hydrocarbons:
It is assumed that the plant is using either Natural Gas or LPG for fuel in the Air Heating furnace, quantity is 32.6 GJ/hour=70.80 kg/hr=.019 kg/s. This much HC if leaks from piping to the atmosphere for 10 minutes =600 sec will be equal to 11.8 kg, which cannot cause the fire and explosion of the magnitude as happened.
C.3 High pressure Cellulose cake piping :
Hazard is only high pressure but temperature is low so Fire hazard possibility can be ruled out.
Process Hazards:
c.4 Process Conditions in the furnace
c.5 Process Conditions in Spray Dryer
c.6 Process Conditions in Cyclone Separator/ in the quarantine storage
C.4 Process Conditions in the furnace
Following potential Hazards are possible
Hazard Conditions | Results |
1.Air Heating Furnace Tube rupture | Air will enter into the Furnace casing, Fire and explosion may happen pressure expected 2.34 Atm, explosion vents (if provided) would have released pressure to atmosphere. But this should not have created damage to the extent happened. |
2. Air temperature increases beyond 4000 C due to malfunction of TIC of the Air Preheater Furnace | There may be Fire in Spray Dryer due to combustion of cellulose in spray dryer see c.5 (2) later. |
C.5 Process Conditions in the Spray Dryer
Following potential Hazards are possible
Hazard Conditions | Results |
1.Flow of Cellulose Cake(feed to spray dryer) stops | Air temperature increases beyond 2400 C but may not reach 4000 C. Considering that high Air Temperature due to heat sink loss will reduce firing load in the Furnace due to TIC at air outlet of Furnace is working. But the pressure in the spray dryer will increase corresponding to maximum air temperature. |
2. Air temperature increases beyond 4000 C due to malfunction of TIC of the Air heater Furnace controlling furnace firing. | There may be Fire in Spray Dryer followed by Explosion due to Cellulose Combustion. Impact pressure could be 4.02 Atm at a distance of 10 m from explosion epicentre. |
3.Flow of cellulose product stops | Air temperature increases beyond 2400 C but may not reach 4000C However, the pressure in the spray dryer will increase due to Air Heating. Reasoning is same as in c.5 (1) above. |
C.6 Process Conditions in Cyclone Separator/ in the quarantine storage
Following potential Hazard are possible
Hazard Conditions | Results |
1. Combustible dust cloud of MCC gets mixed with air, gets ignited by an ignition source: Electric Motor or high heat source or static spark exceeding Minimum Ignition Energy value. | There may be Fire in Cyclone Separator or in quarantine storage followed by Explosion due to Cellulose Combustion. Impact pressure could be 2.0 Atm at a distance of 10 m from explosion epicentre. |
D: Conclusion:
As per technical Analysis Fire followed by Explosion scenarios are as under:
D.1 Tube rupture in Air Heater Furnace, pressure generated: 2.34 ATM
D.2 Spray Dryer Fire and Explosion of 4.02 Atmosphere magnitude.
D.3 Combustion dust of MCC getting mixed with air, ignited and causing Fire and Explosion of 2.0 ATM magnitude.
Based on physical effects of Fire and Explosion at Sigachi Plant (on 30 June 2025 at 9.00 am), Spary Dryer Fire and Explosion is the credible cause.