Abstract
A Major Accident Hazard (MAH) is a source of danger that has the potential to cause a major incident, involving multiple fatalities and/or significant damage to plant, equipment or the environment. India is experiencing high rate of fatal accidents in the refineries. The present paper compares the MAH handling strategies in India vs US as some sample cases to analyse the causes of higher accident fatality rates in India. This analysis highlights the different regulatory, Process Safety Management, Environment Control, and Human Behaviour towards safety in two countries; and also regulations in US to enforce the Safety and Environment rules strictly. Analysis is based on actual MAH incidents in India (OISD Accident Reports) and Chemical Safety Bureau (CSB) US reports. A literature review has been conducted to gather information related to the actual fires and explosions in refineries and oil terminals in India and US. In the context of refining operations as adopted in US, “Process Safety” refers to the prevention and mitigation of unintentional releases of potentially dangerous materials or energy from the refining process. On the other hand, “Personal Safety,” as adopted in India, is sometimes referred to as Occupational Safety, focuses on hazards that are more directly related to individual workers safety, health and hygiene. Such accidents are usually associated with a hazard that is close to workers. Process Safety programs focus on, among other things, the design and engineering of facilities; hazard assessments; management of change; inspection, testing, and maintenance of equipment; effective alarms; effective process control; procedures; training of personnel; and human factors. Protection against a Personal Safety hazard is both relatively simple and, for the most part, at least nominally under the control of the potentially affected worker. A detailed analysis has been done on various technological, regulatory and HSE frame work deficiencies for poor safety performance in India. The suggestions are provided to improve safety performance of Indian refineries.
1. INTRODUCTION
A Major Accident Hazard (MAH) is a source of danger that has the potential to cause a major incident, involving multiple fatalities and/or significant damage to plant, equipment or the environment. Year wise MAH fatalities in an organization indicates the level of safe and healthy working environment in the setup. The following graph compares the year wise fatalities data of Indian refineries vs those of US refineries
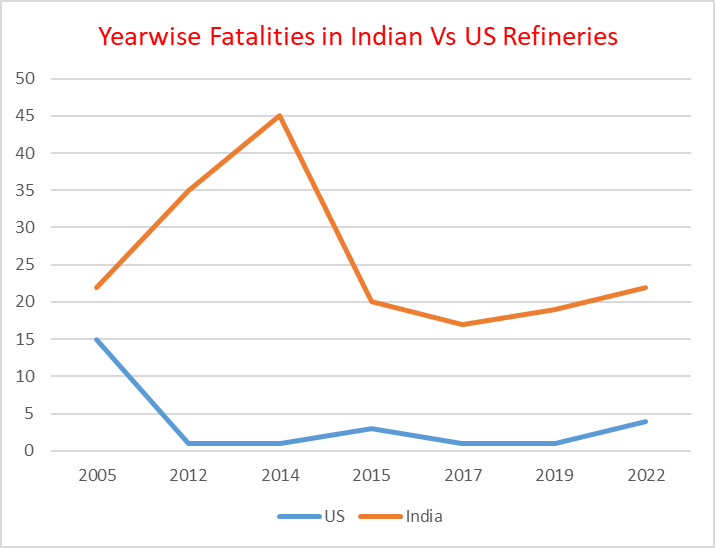
Ref:
1. Indian refineries Fatalities Data are based on OISD Data Base
2. US refineries fatalities Data are based on CSB, ARIA, and other internet sources
Although number of refineries and refining capacity in US are more than 3 times that of India the average MAH deaths in US refineries are 3.7 compared to 25 in India as per following table:
Parameter | US | India |
Refining Capacity | 875 MMTPA | 256.7 MMTPA |
Number of Refineries | 130 | 23 |
Average Fatalities | 3.7 | 25 |
The above is due to the fact that Process safety in US refineries is more robust and comprehensive compared to Indian refineries, due to factors like more stringent regulations, advanced technologies, and a culture of safety. While both types of refineries face risks inherent to handling hazardous substances, Indian refineries have been observed using more traditional obsolete safety measures that may not address the issues of process safety management as comprehensively.
2. CAUSES OF HIGHER MAH FATALITIES IN INDIAN REFINERIES IN LAST FIVE YEARS
Higher accident fatalities in Indian refineries may be attributed to the following causes shown in the PI diagram:
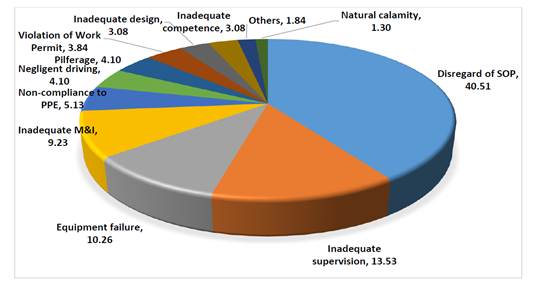
Reference: Report of the Working Group on Safety in Indian Petroleum Sector 2023, (OISD Data Base)
From the analysis, the primary cause of accidents (40.5%) was observed to be disregard/ non-adherence to Standard Operating Procedures (SOP) followed by inadequate supervision (13.53%), equipment failures (10.26%), inadequate maintenance & inspection (9.23%). These four factors alone contributed to 73.53 % of the total incidents. Hence, fool-proof mechanism for adherence to SOP, effective supervision and proper upkeep of the facilities are the key areas for improving HSE performance in India. These data pertain to last 5 years but it is pertinent to see hard realities of Indian refineries in larger spectrum of 20-25 years with following safety related issues:
2.1 Disregard to SOP:
As per author’s experience of working in refineries in India and Oil/Gas plants abroad disregard to SOP by the operators can be attributed to:
- The working environment has eroded over time to one that is characterized by resistance to change and by lack of trust, motivation, and a sense of purpose. This environment, coupled with unclear expectations about supervisory and management behaviours have led to rules and SOPs not being followed consistently, a lack of rigor, and individuals feeling disempowered from suggesting or initiating improvements.
- SOPs are not available for some of the critical activities’ related hazards or some of the scenarios.
- Ambiguity, lack of clarity or inconsistency in available SOPs along with lack of threshold values of hazardous substances and hazardous conditions.
- Inadequate understanding of the SOPs. Indian norms developed by PGNRB and OISD are adopted from various old and obsolete sources and their technical credence is suspect viz. Assumption Register of QRA and inter unit and inter equipment distances per OISD118 do fail in Fire/Explosion /Toxic Gas consequence results.
- Revisions to SOPs are not done in spite of refineries Risk rising due to increased complexity, constrained spaces, outsourcing operating jobs. Hazards and SOPS are not communicated or percolated to the work force. SOPs are not reviewed/ revised after plant modifications/ revamp/ incident etc. as per MOC (Management of Change). Moreover, SOPs are not reviewed/ revised at the stipulated frequency or learnings from past incidents are not included in the SOPS.
- Ineffective document control resulting in multiple/ outdated versions of SOPs in circulation leading to errors.
- Lack of clarity in Roles & Responsibilities and escalation metrics in SOPs.
- Deviations in actual working practices from the SOPs. Overconfidence of the operating crew or short cuts taken disregarding the SOPs.
- Lack of awareness or necessary management controls to ensure SOP compliance without deviations
2.1.1 Some Live Examples of SOP disregard in Indian Oil Sector:
2.1.1.1. Jaipur IOCL Terminal Fire and Explosion on 29 October 2009.
a. In the evening shift of October 29, 2009, the Indian Oil Corporation (Petroleum Oil and Lubricants) Terminal at Sanganer in Jaipur, India was preparing to transfer Motor Sprit to the neighbouring BPCL terminal a routine operation.
b. In the process of lining up the MS tank 401A at about 6.10 PM, a huge leak of MS (Gasoline) took place as a jet of liquid from the Hammer Blind on the delivery line of the Tank leading to the MS pump. On the tank outlet line connected to delivery pump, the MOV got inadvertently opened when Hammer Blind was already open. SOP should be that both MOV and Hammer blind should remain closed initially. First HOV (Hand Operated Valve) at d/s of Hammer Blind should open. Then Hammer Blind should open and finally MOV should open slowly to create enough flow to start the despatch pump, see the diagram on next page.
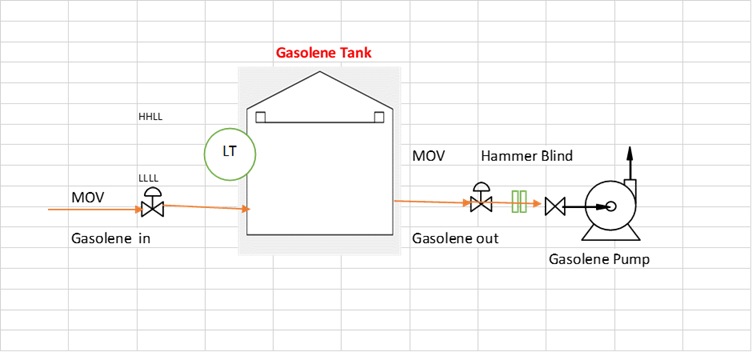
c. The liquid MS which rapidly generated vapours soon overwhelmed and incapacitated the operators carrying out the line-up operation. Operators and shift in-charge were unaware what to do when the leak through about 10’’ hammer blind continued. Because there was no SOP.
d. With none of the operating crew being available any more for initiating control actions, the leak continued unabated.
e. After about an hour and 15 minutes (75 minutes) of the leak started, there was a massive explosion followed by a huge fireball covering the entire installations. It is estimated that in this one hour and 15 or 20 minutes of uncontrolled leak about 1000 tons of MS could have escaped out which could have generated enough vapour to cause an explosion with a equivalence of 20 Tons of TNT.
The source of ignition, which triggered explosion and fire could be from one of the non- flame proof equipment in the Administrative Block, or from the vehicle being started in the installation. Contours of consequences w.r.t. explosion shock waves and LFL of vapour cloud based on information are drawn on the next page.
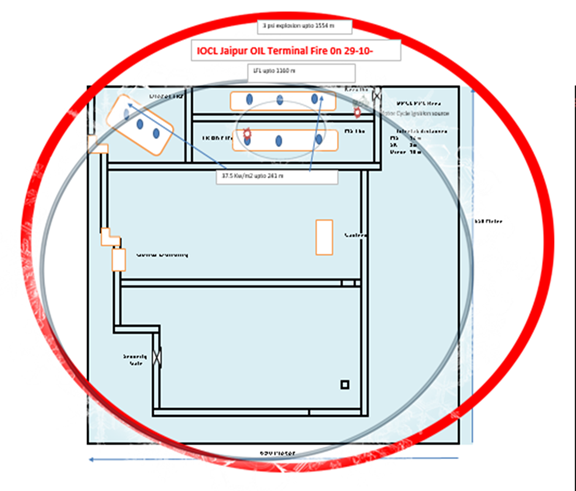
Hazard Contours
f. This Fire/Explosion killed about 11 people, injured 300 and about 60000 KL of petroleum products were deliberately burnt.
g. Root cause of the MAH was open MOV valve and open Hammer Blind on the discharge line of the MS tank connected to the delivery pump.
Oil terminals MAH handling strategies in US, UK vs India
CAPECO Terminal US | Buncefield Terminal,UK | Jaipur Oil Terminal ,India | |
Incident Date | October 23, 2009 | December 11, 2005 | October 29,2009 |
Time of explosion | 12:23 am | 6:00 am | 7.35 pm |
Number of persons killed | 0 | 0 | 2 |
Number of employees injuries | 0 | 0 | Not Known |
Number of public injuries | 3 | 40 | 200 |
Product involved in Loss of Containment | Unleaded Gasoline | Unleaded Gasoline | Unleaded Gasoline |
Storage capacity of site | 283,233 tons | 194,000 tons | 60000 KL |
Involved Tank storage capacity | 1900KL | 6000 KL | 2000 KL |
Explosion Richter Scale | 2.9 | 2.4 | 3psi |
Estimated area of vapour cloud | 107.2 acres (657m*657m) | 32 acres (360 m*360m) | 110 acres (696m*696m) |
Number of tanks engulfed in fire | 17 | 20 | 10 |
Number of days to contain fire | 2.75 | 5.0 | 11 |
MAH initiating Tank | Tank # 409 Overfill | Tank # 912 Overfill | TK 401A discharge line 10” Hammer blind leak |
Estimated volume | Overfill 757 KL of gasoline Tank overflowed for 27 minutes | Overfill 250 KL of gasoline | Estimated leak 1200 KL |
Volume of contaminated water released to environment | 647 KL of collected oil; 22,000 KL of contact water (the oil percolated into a water bay) | 800 KL | Not estimated |
MAH sequence of events | 1. The Cape Bruny cargo ship arrived on October 21, 2009 to unload 11.5 million gallons of unleaded gasoline. 2. Largest Tank 107 did not have ullage. So the TK 409 was lined. 3. Between the 11 p.m. and 12 a.m., Tank 409 overflowed, releasing gasoline to atmosphere which formed a vapour cloud and a liquid pool. 4. The operator contacted the dock operator to halt the flow of gasoline. 5. At 12:23 a.m., ignition of the vapour cloud occurred in WWT area. About seven seconds after ignition, the vapour cloud exploded, creating a pressure wave that damaged hundreds of homes and businesses up to 1.25 miles from the site. The fire propagated through the vapour cloud and ignited multiple subsequent tank explosions registering 2.9 on the Richter scale. 6. Commonwealth of Puerto Rico and the US mainland, local fire departments with assistance from an industrial firefighting company took 66 hours to extinguish the fire after the explosion. As a result, 17 of the 48 tanks burned. | 1.Teekay co.pipeline started flow of petrol to Tank 912 arrive at Tank 912 at about 05:30 GMT on 11 December. The safety systems in place to shut off the supply of petrol to the tank to prevent overfilling failed to operate. Petrol cascaded down the side of the tank, collecting Tank bund. 2. About 300 tonnes of petrol escaped from the tank, about 10% of which turned to vapour mixing with air became flammable. 3. Between 05.30 to 06.00GMT Sunday 11 December 2005,the vapour cloud was seen. 4. At 06:01 GMT @11 December 2005, the first of a series of explosions took place.These explosions caused a huge fire which engulfed 20 large storage tanks over a large part of the Buncefield depot. The fire burned for five days, destroying most of the depot. | 1. MS tank 401A line up to Despatch Pump at on 29 th October 2009@ 6.10 PM, a huge leak of MS (Gasoline) took place from the Hammer Blind the MOV got inadvertently opened when Hammer Blind was already open. 2. The liquid MS which rapidly generated vapours. 3. After 75 minutes) of the leak, there was a massive explosion followed by a huge fireball covering the entire installations. In uncontrolled leak about 1000 tons of MS could have escaped enough vapour to cause an explosion with a 20 Tons of TNT equivalence. |
Ignition source | Ignition and initial flash fire in the WWT area | Probable: pump house, emergency generator room, car engines etc. | The probable ignition source was a bike on north east of the Tank |
Response assessment | Limited emergency preparedness | 7. The 1000 firefighters too took 32 hours to extinguish the main blaze, although some of the smaller tanks were still burning. Overall, 750 000 litres of foam concentrate and 55 million litres of water were used. | 1.Insufficient equipment 2.Insufficient preplanning with local fire department or fire training 3.Limited emergency preparedness |
Root cause | 1. Operating philosophy of filling tanks to maxm at the cost of safety. 2.Lack of formal procedures for Terminal operations | Failure of the independent AOPS(Automatic Overflow protection System) | SOP violations, |
Contributing cause Regulatory consideration | Not considered high-hazard Facility. | Considered high-hazard facility. | Not considered high-hazard facility |
Reference: 1. CAPECO and Buncefield Reports of CSB
2. Jaipur Oil Terminal: OISD Report and MB Lal report
Salient Comparison of the Fires/Explosion handling as above in US, UK vs India
- All three cases pertain to Oil terminals involving Loss of Containment of Gasoline, making vapours, vapours mixing with air, getting ignited by ignition sources within boundaries of the Oil terminal and causing damage to surroundings through explosions.
- Impacts of Fire and Explosions in US and UK were less severe as compared to Jaipur Explosion in terms of deaths and injuries inside the terminal and for general public. This may be attributed to competent manpower in large number available in US and UK plants for firefighting as compared to Jaipur terminal.
- UK considers Gasoline as hazardous material so it was better equipped technologically to fight the fire than US, which till then did not consider it as hazardous substance. India also does not consider Gasoline as Hazardous Substance.
- The Accident Investigation authorities in US and UK had recommended implementation of Process Safety Management in Oil terminals but in India it is not a Regulatory policy guideline.
- Domino effect and Multi Tank Fires are not considered in Fire Fighting philosophies throughout the world. NFPA firefighting water requirement of 4 hrs. is inadequate and obsolete. OISD-117 requirement of considering 1 fire at a time in oil terminal is also inadequate and obsolete.
- India and US did not learn the lessons from Buncefield fire and explosion and repeated the same mistakes or did not do the planning for such kind of MAH.
2.1.1 .2. Benzene tanks Fires at Gujarat Refinery
- SOP of Gujarat refinery did not have Benzene Fire and Explosion scenario handling guidelines. In one such incident in the refinery, already crowded with HC storage tanks, Fire and Explosion happened inside a Benzene Tank due to static spark fire generated inside the tank. This Fire was followed by Explosion and threw away the Tank Roof and the dipping operator (standing on the roof) died standing thereon, body found 20 meter away from the tank on the ground.
- By Domino effect this Fire impacted and heated adjacent Benzene Tank, over pressured the tank and throwing its roof 160 m away from the tank. The fire in first tank continued for 5 hours to heat the adjacent tank. Foam injection in the burning tank was found ineffective.
- Root cause was ignorance of operating staff in not complying SOP stating that no activity in the tank (pump in, pump out or dipping) shall be done for minimum 30 minutes (Benzene Relaxation time) after Benzene pumped in. It appears it was not written in SOP clearly as OISD standards also did not specify it lucidly.
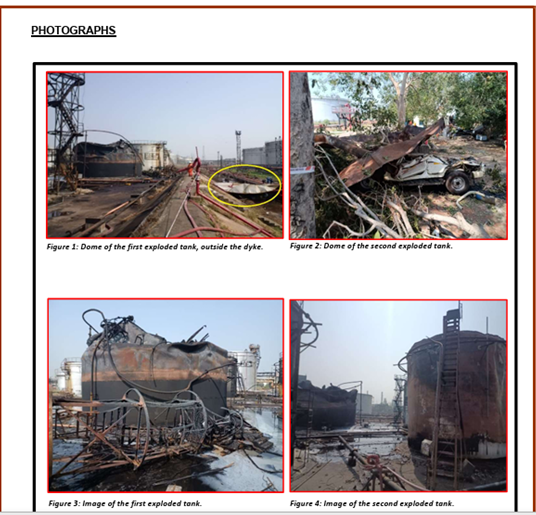
Benzene Tanks Layout Plan at Gujarat Refinery
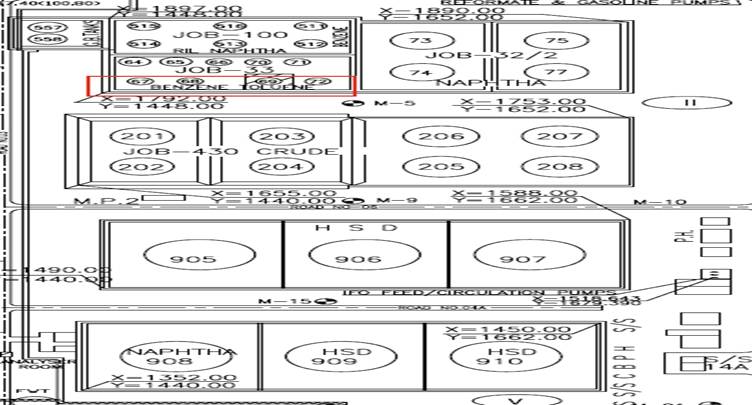
Spark Ignition Fire in Tank MAH handling strategies in US vs India
Barton Solvents Wichita facility in Valley Centre, Kansas,US | Gujarat Refinery | |
Incident Date | July 17, 2007 | November 11,2024 |
Time of explosion | 9.00 am | 3.50 pm |
Number of persons killed | 0 | 2 |
Number employee injuries | 0 | 1 |
Number of public injuries | 12 | Not Known |
TKs involved in Fire/Explosion | 3 | 2 |
Product being filled | Varnish Makers’ and Painters’ (VM&P) naphtha. | Benzene |
Material Safety Data Sheets (MSDSs) | MSDSs do not typically communicate static ignition hazard. Companies should contact the manufacturer (or an expert familiar with the relevant consensus guidance) for this information. | |
Storage capacity of site | Approximately 20,000 gallons of flammable liquid were released. The tank farm included 43 above-ground storage tanks with capacities ranging from 3,000 to 20,000 gallons. Tank heights ranged from approximately 15 to 40 feet. | Not Known |
Tank storage capacity | 50 KL | 1000 KL |
Vapor cloud explosion | Yes | Yes |
Sequence of Events | Barton pumped the VM&P naphtha from three separate compartments in the tanker-trailer to the VM&P tank. Air pockets were introduced into the fill piping, and then transferred into the tank when the transfer hose was reconnected to the tanker-trailer after compartments were changed. Studies have found that static electricity accumulates rapidly during pump start up when nonconductive liquids are transferred to storage tanks (Walmsley, 1996). The initial explosion occurred on July 17, 2007, at about 9 a.m., soon after the transfer start of the final compartment of a tanker-trailer containing VM&P naphtha into a 15,000 gallon above-ground storage tank. The explosion sent the VM&P tank rocketing into the air, trailing a cloud of smoke and fire from the burning liquid; it landed approximately 130 feet away. Fire and explosion was experienced several miles away. Within moments, two more tanks ruptured and released their contents into the rapidly escalating fire. . | A sampler went for sampling in a benzene storage tank (capacity 1000 KL with actual material approx.523 KL) after receipt of benzene. While the sampler was on top of the tank, an explosion and fire occurred, skyrocketing the fixed roof of the tank. The sampler body was found near the roof that landed around 20 m away from the tank, just outside the dyke. Another benzene tank (capacity 400 KL with actual material approx. 48 KL) in the same dyke exploded about five hours later while the firefighting was in progress. The roof of the second tank landed around 160m away, on a tree and a parked vehicle, which was crushed. Where the second tank roof landed, a canteen worker fell unconscious and the Refinery Shift Manager suffered injuries. The canteen worker later succumbed. The fire was completely extinguished after about 10 hours of firefighting, with support of mutual aid partners. |
Impact of Explosion | Eleven residents and one firefighter received medical treatment. The incident triggered an evacuation of 6,000 residents and destroyed the tank farm. | Information not available |
Explosion | In this case, the static electricity accumulation was likely exacerbated by the air pockets and the likely presence of suspended sediment and water in the tank. In addition, the VM&P tank was approximately 30 percent filled at the time of the explosion, which would have produced a liquid surface potential (voltage) close to the maximum expected during filling. | The first explosion was caused by the confined vapour cloud explosion between the floating roof deck and the fixed roof ignited most likely by spark emanating from the dip hatch lid (non-spark proof) or the discharge of static charge of benzene liquid (accumulated during the receipt of material) at the time of sampling activity. The second explosion occurred due to boiling of material in the second tank, aggravated during the foam application interruption at the incident site. |
Richter Scale | Not measured | Not measured |
Estimated area of vapour cloud | Not measured | Not Measured |
Number of tanks engulfed in fire | 3 | 2 |
Number of hours to contain fire | Not available | 10 |
Recommendation | Add a Non-flammable, Nonreactive (inert) Gas to Tank Head Spaces. | Plot plan of Benzene Tanks hampered firefighting as Fire Fighting Access was available only from south side of tanks. |
Contributing cause Regulatory consideration | Not considered high-hazard facility | Not considered high-hazard facility |
Reference: 1.Barton Solvents Wichita facility in Valley Centre, Kansas: CSB Accident Report
2. Gujarat Refinery: OISD Accident Report
Salient Comparison of the Fires/Explosion MAH handling due to static spark
- US case pertains to Oil terminal and Indian Case is related to Gujarat refinery both involving Static Spark ignition vulnerable substances catching fire inside tank in presence of air and causing explosion.
- Impact of Fire and Explosions in US was less severe as compared to Gujarat refinery Benzene tank in terms of quantity of substance involved, deaths and injuries inside the terminal. This may be attributed to competent manpower in large number available in US terminal for firefighting as compared to Jaipur terminal.
- The US Accident Investigation authorities had recommended implementation of Process Safety Management in Oil terminals but in India it is not a Regulatory policy guideline.
- Domino effect and Multi Tank Fires are not considered in Fire Fighting philosophies throughout the world.
- India did not learn the lessons from US fire and explosion and repeated the same mistakes or did not do the planning for such kind of MAH.
- The OISD investigation report for Gujarat Refinery Benzene tank Root Cause conclusions was possibility of the discharge of static charge of benzene liquid (accumulated during the receipt of material) at the time of sampling activity.
In US the ROOT cause is concluded after detailed technical studies but in India this is not done.
2.2 Inadequate Supervision
Inadequate supervision has been found due to the person concerned and the working environment. Individual reasons include lack of competence, application of mind, commitment to safety or clarity on the work processes and associated hazards.
External reasons include overload, stresses, fatigue, multiple simultaneously running tasks with overlapping responsibilities, inadequate management processes, lack of SOPs, lack of adequate resources, organization culture etc.
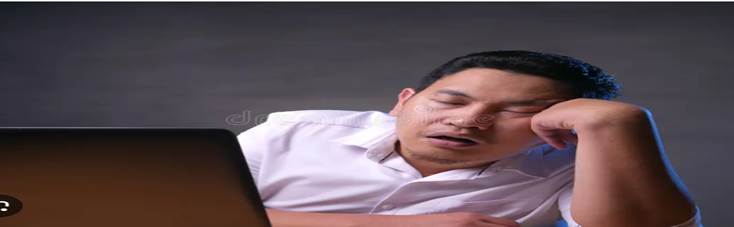
Reference: Internet free data
Following issues of Inadequate Supervision need to be addressed:
Poor quality of supervision
- Supervisors fail to perform supervision in accordance with the requirements of rules and regulations
- Failure to provide supervision and guidance
Inappropriate Supervision due to managerial issues
- Inadequate staffing or work arrangements
- Improper arrangement of work windows( extended hours working)
- Inadequate risk analysis
Supervisory violations
- Supervisors deliberately ignore or violate existing rules and regulations
- Supervisors fail to perform supervision as required
2.3 Equipment Failures
The analysis has found that most areas had insufficient resources to conduct the needed Root Cause Failure Analysis (RCFA) for equipment problems, and that most action items are considered to linger till next big shutdown or Annual Turn Around in the hope of maintaining or increasing production. In one refinery lower pressure rating hose was used to transfer Naphtha at the discharge of the pump (on the basis of advice of Contractor staff) as a result the hose pipe ruptured ,Naphtha leaked ,vapour cloud caught fire and explosion occurred causing injuries to persons in the area.
Safety Critical Equipment and Systems maintenance/ calibration/ testing regular checking for their survivability during MAH are not done. In case of Jaipur Terminal Fire 2009, the Fire Fighting System was found incapable.
2.4 Asset integrity management (AIM)
Asset Integrity Management is a set of techniques applied through industrial plants with the purpose of developing, implementing, and continuously improving the integrity of industrial assets in order to maintain productivity, reduce downtime, prevent accidents and generate greater safety for field operators. Following AIM problems are prevalent in Indian Refineries:
- Not adhering to PMS schedule
- Delay in handing equipment for Inspection
- Overstretching equipment run
- Postponement of Tank M&I & Annual Turnaround schedule
- Higher frequency of Mechanical seal failures
- Improper maintenance practices
- Impaired safety critical items for long time
- Integrity of flame proof fittings not maintained
- Not undertaking proper inspection upon repair
- Many a times for spare equipment the switchover schedule is not followed due to lethargic attitude of operation and maintenance staff.
- The AIM staff is not well trained and rely on OEMs.
- Maintenance Philosophy constraints
- Risk management philosophy if Risk Based Inspection and Maintenance is not clear.
- Divergence in OEM, Process Licensor Philosophy and Risk Based Inspection.
2.4.1 Asset Integrity Management System noncompliance Fire Accident
On 31stMay a major fire incident took place at CDU and VDU of Numaligarh refinery due to sudden failure of crude booster pump from its casing plate to shut down the refinery. The fire lasted for 4 hours which caused extensive damage to pumps, motors, technological structures, pipelines and allied instrumentation and electrical cables. There was no injury/loss of life due to fire incident. Root causes were:
1. Failure of the impeller lock nut caused rubbing of the impeller against the pump casing and consequential fire.
2. Improper trip setting of the pump motor which does not allow pump to trip at higher load.
3.0 HARD FACTS IN INDIAN REFINERIES CAUSING HIGHER MAH
Sl No. | Issue | Actual situation in India | Actual situation in US and Europe |
1 | Hazard analysis for Hazardous substances like Methane, Flammable gases and liquids, Chlorine, Ammonia, H2S is not done as part of Hazop for QRA and for oil terminal. | Yes, not being done as a matter of policy so higher frequency of MAH | Hazard Analysis incorporation under Process Safety Management is under examination in US and already existing for Europe |
2 | Deliberate Burning of HC tanks should Fire Fighting systems fails | Practised when needed though not permitted per Environmental Act. No penalty for deliberate burning. | Not allowed, Penalty is imposed if approval is not taken. |
3 | Practice of learning from the experience of others rather than learning the hard way. Learnings must pass on to the next generation. | Practice is not followed. | Practice is partially followed. |
4 | Domino effect of fire from one equipment to another equipment | Not considered | Now under consideration for Hazard examination |
5 | OISD and NFPA 10 Fire Water Demand for refinery should be maximum 4 hours | Reality is that Multi Tank Fires continue beyond 4 hours as in Gujarat Refinery Benzene Tank fires | Multi Tank Fires continue beyond 4 hours and as high as 5-6 days |
6 | NFPA design based foam Pourers effectively fight the tank surface fire | Foam Pourers get damaged during fire and explosion but no remedial measure is thought of. | Foam Pourers get damaged during fire and explosion but no remedial is measure thought of. |
7 | Existing regulatory and monitoring mechanisms do not support Process Safety Management implementation in refineries and oil terminals | Indian Government Policy does not support | US and Europe/UK Govts. Policies support |
8 | Human Error issues will increase MAH due to inadequate competence and supervision owing to outsourcing of refinery and oil terminal operations. | No actions envisaged | Yes, but actions are in pipeline to address the issues |
9 | Probability of MAH Risk for operating worker is maximum 10E-04/year and 10E-06/year for public outside | These are theoretical values and Risk is much higher as per past 10-15 years of MAH records | These are theoretical values and Risk is much higher as per past 10-15 years of MAH records but lower than India |
10 | Release diameter for equipment is 25 mm to 50 mm for QRA calculations | In actual MAH release diameters are 100 mm to 250 mm | In actual MAH release diameters are 100 mm to 250 mm |
11 | Accident report should indicate total hazardous substance release quantity | Not done | Done |
12 | Accident report should indicate Environment impact to Air, Water and soil along with quantities | Not Done | Done |
13 | Accident report should indicate hazardous events sequential timeline of MAH | Not Done | Done |
14 | Corroboration of Accidents with Consequence modelling and/or QRA | Not Done | Done |
15 | If the design is based on international standards like ASME, API, NFA etc. it can be considered to be Inherently Safe Design | Accepted | Not accepted. Inherent Safe Design Analysis is done. |
16 | Level – III emergency or an incident with off-site impact which could be catastrophic and is likely to affect the population, property and environment inside and outside the installation, and management and control is done by district administration. Although the Level-III emergency falls under the purview of District Authority but till they step in, it should be responsibility of the unit to manage the emergency. | Accepted but refinery and local authorities have failed in fighting multi tank fires. | Multi Tanks firefighting needs intensive training of Refinery/Oil Terminal management as well as outside firefighting staff. |
17 | A radiation thermal intensity of 20-22 Kw/m2 (for Benzene Tank vaporization in about 7 hours per Gujarat Benzene Tank fire ) for 10E-05/year should be checked for Cooling the tank on Fire and adjacent Tank for cooling be compared with OISD 116 and NFPA norms for cooling water and foam injection. | Not done | Being done on selective basis |
18. | Firefighting of tanks exceeding 20 m diameter have caused problems in many cases, especially larger than 45 m in diameter. Standards, NFPA 11 provide very limited guidance on how to extrapolate fire protection guidelines from smaller tanks to the huge fire risks of today. It is not fully known what type of equipment, type of foam, application rate and tactics should be used. Ref: Tank Fires, Review of fire incidents 1951–2003,BRANDFORSK Project 513-021 | NFPA guidance still follows. | Issues are being studied. |
19. | Assumption that the human operator will “save the day” holds good. The mental model of the system operator plays an important role in accidents. | Holds good in India | Knowledge, skill and practical experience of the operators are analysed. |
20. | Reports of working Groups or Monitoring agencies are implemented. | Report of the Working Groups on Safety in Indian Petroleum Sector 2023 rejected some vital recommendations for Policy reasons | Reports of working Groups or Monitoring agencies are implemented. |
21. | Accident Investigation Report should identify Root Cause as the first Initiating Event viz. Loss of Containment for first MAH, second MAH due to domino effect may have the consequence of first MAH as root cause. | Root cause determination is vague. Sometimes, the MAH final result is considered as a root Cause. | Root cause is confirmed based on first Initiating Event of Consequence modelling |
4.0 APPROACHES FOR SAFETY IMPROVEMENT IN INDIAN REFINERIES:
Report of the Working Group on Safety in Indian Petroleum Sector 2023 did recognize the Process Safety Management superiority and effectiveness in improving the safety level in refineries but did not categorically recommended the Process Safety Management implementation in Indian refineries due to some policy constraints. Following are the important recommendations based on US Baker Panel Report:
4.1.1 Refiners should adopt Process Safety against Occupational Safety
The safety policies/plans adopted hitherto by Indian refineries do not address holistically the issues of Process Safety and Management as practised in US and Europe, leading to higher accident frequencies in India. Indian Refiners aim is to earn more profits than the safety improvements.
Process Safety programs focus on the design and engineering of facilities, hazard assessments, management of change, inspection, testing, and maintenance of equipment, effective alarms, process control, procedures, training of personnel, and human factors.
Baker Panel believes, that the underlying or “root” causes of the large majority of personal and process accidents are deficiencies in the systems that a facility uses to prevent these two classes of accidents. The Panel believes, that the presence of an effective Personal Safety Management system does not ensure the presence of an effective Process Safety Management system.
4.1.2 As per current project philosophy in India
For installing brownfield project on the existing plot of running refinery, the RRA/QRA of only new Brownfield project is done without taking QRA of an integrated facility (existing plus new facilities) of increased hazardous inventory on the plot, reduced inter tank and inter unit spacing and considering Domino Effect.
Although, some RRA reports are available in public domain in India but on review of these RRA/QRA reports, one can find many deficiencies. RRA/QRA Assumptions Register indicates selective data usage and adverse Consequence results do not warrant the preventive/mitigating /recovery barriers requirements.
4.1.3 Requirement of making stringent project approval standards and upgrading skill and competence of approvers in India
In the United States, refinery project approvals typically involve officers from the Environmental Protection Agency (EPA), the Department of Energy (DOE), and potentially state and local agencies. These officials require expertise in environmental regulations, energy policy, safety and engineering to assess project proposals and ensure compliance.
In India we cannot expect rigorous technical scrutiny of Refinery Project Proposals due to lack of competence and expertise amongst approving authorities about modern tools and techniques of Process Safety.
4.1.4 Accident Investigation Reports in India:
These reports are generally prepared by a team of OISD and some representatives of Operating Oil Companies other than involved in the Accident. These reports do not report following information like U.S. Chemical Safety Board (CSB) an independent, non-regulatory federal agency that investigates the root causes of major chemical incidents.
In India an Investigation Report does not contain the following information, which should be provided:
4.1.4.1 Released hazardous substance quantities: flammable, toxic gas release
4.1.4.2 During toxic gas (H2S, Benzene, SO2 etc,) release, if general public was warned and evacuated on hazards and precautionary measures to be taken is seldom known.
4.1.4.3 Human Failure detailed analysis should be part of the report with recommendations for knowledge enrichment, attitudinal changes and behavioural training. Simply telling SOP was not complied is inadequate. If SOP was available and he was asked to go through and understood and declared yes, should be incorporated.
4.1.4.4 In most of fatalities, contract workers are the causalities due to inadequate training on operations and hazard. In such cases, the Operation Engineer shall carry out a Job Hazard Analysis and explain the operator implications fully and get a feedback. Such documents should be part of Investigation Report.
4.1.4.5 There is no simulation or situation creation of the Major Accident Event. This should be available.
5. Conclusion:
A concerning situation in India is that there seems to be no learnings from accidents both in India and abroad, because the concerned agencies do not probe root causes. Sometimes, consequence of the accident is considered as the Root Cause to shrug off the responsibility. The government agencies as well as owner of the refineries want to close the accident case after paying compensation to the kin of deceased. In India there is no will either at Government or refinery management levels to adopt the Process Safety Management System as prevailing in US and Europe. Occupational Safety as practised in India cannot prevent the Major Accident Hazard.
US has adopted the Process Safety Management and India should adopt it without further delay to reduce the fatality rates in refinery accidents.